Hello. I’m James, and I’m an RV nerd.
It’s true. On any given Saturday, while the rest of the clan is out taking the grandchildren to the “interactive farm”, I’m probably underneath our RV. Maybe I’m checking for hairline cracks in the ABS pipes. But it’s more likely that I’m just hanging out down there – thinking up new projects.
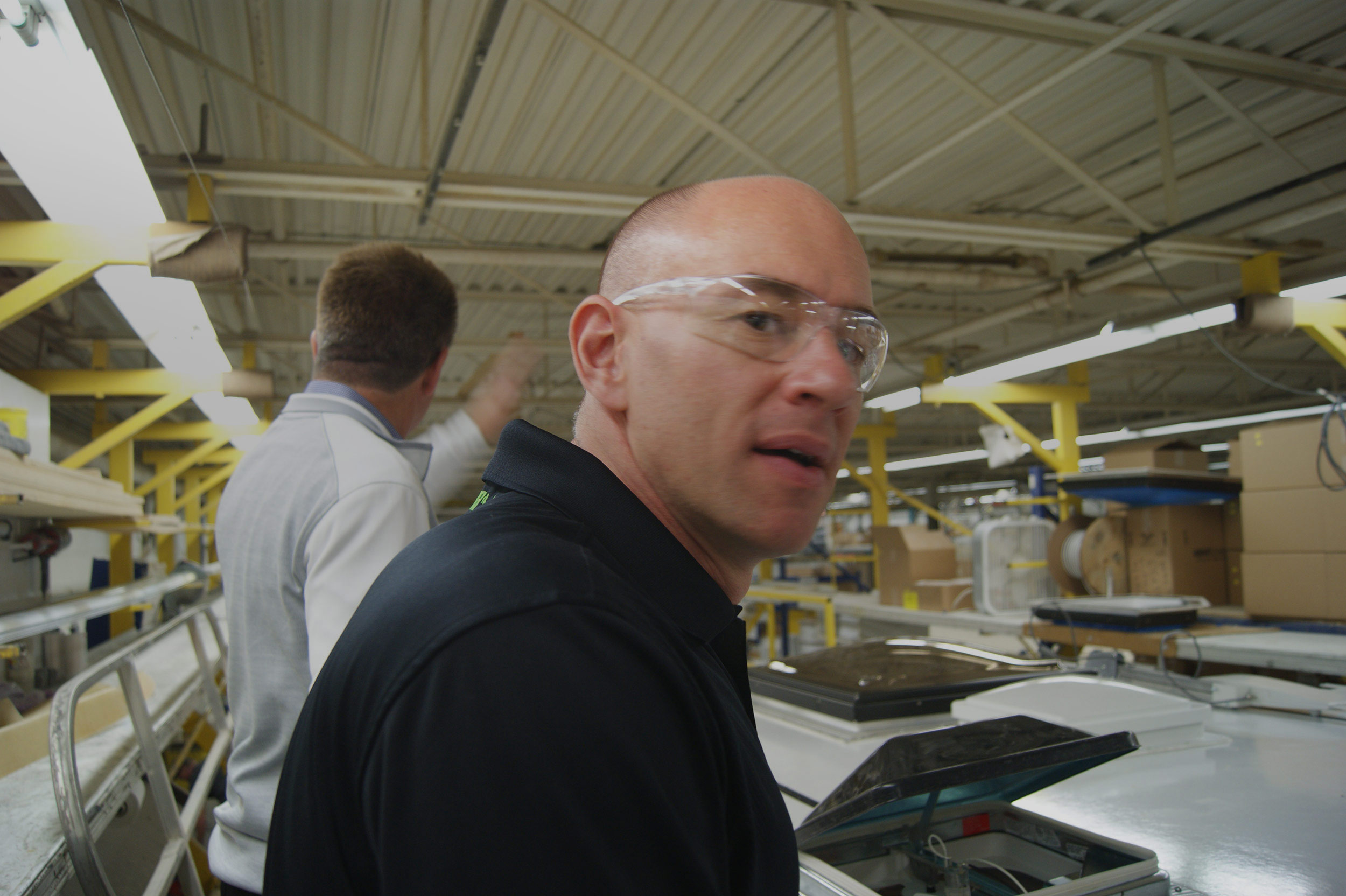
Stef thinks this is weird, but it all seems completely normal to me.
Knowing that, it shouldn’t surprise you that on our recent road trip, I convinced Stef to take a very minor, 1200 mile detour to Winkler Manitoba to check out the Leisure Travel Vans factory. This was a chance to see the RVs before they were finished, to understand why they’re built as they are, to see inside the walls, so to speak, and to ask questions. How could we not go?!
We were met at the LTV front desk by Dean. If you’re seen his videos and wondered what he’s really like… I’ll tell you, it’s not an act. He’s the same guy in person that you see in the videos and he’s pretty passionate about the Leisure Travel Vans products. His enthusiasm and my inquisitive nerdism (is that even a word?) combined to make what I thought was an extremely informative tour.
Dean, explaining to us that manufacturing the Serenity is much more difficult, because everything has to go into the RV through that door. (Without scratching it up!)
We were at the factory for about four hours. We hit all the major departments, and followed the process from bare chassis to completed RV. You can check out the video for the complete story, but here are a few of the things I remember most from our time there:
Keeping it In-House: One thing that impressed us was that they try to keep as much of the manufacturing process as they can under their roof. We saw them making their own fiberglass molds, all the cabinetry, and even fabricating their own tiny metal brackets. They stop short of mining their own copper and drawing their own wire, but I bet they’ve thought about it.
Attention to Detail: Stef would tell you I’m borderline OCD*, and even I was impressed with some of the little touches I saw going into the RVs they were building. Much of it was things that, as a consumer, you’d never notice. Things like, sealing up openings around wires that most people would think were negligible, and burning 15 person-hours just to mask off a single Free Spirit SS for painting. You may never notice these things, but trust me, you appreciate them. *Stef here: There’s no borderline about it.
Check out Those Walls: For both the Unity and Serenity, they really pay attention to the walls, and to adding the strength where you need it. The Unity walls (and roof… and floor…) are vacuum bonded – where they take multiple layers of material, insulation, metal framing, and resin and fuse them into a single piece. It’s super strong, and you can see the whole process in our video. But what impressed me the most about the vacuum bonding is that they’ve taken the time to figure out where they’ll need to screw things down later – and they reinforce those areas with additional sheet metal that’s also vacuum bonded right inside the rest of the wall. On the Serenity side, they take a similar approach. The walls and roof in the Serenity are solid fiberglass. On the areas they need to reinforce, they use core bonding or solid wood and lay that up and bond it right into the fiberglass walls.
I could keep going on about the factory tour, but Stef will be editing this article for me and I can just picture her eyes glazing over as I extol the virtues of vacuum bonding, so I’ll stop at that.* The rest of the tour is captured in our video. If you own, or are considering purchasing a Leisure Travel Van, you really owe it to yourself to head up to Winkler and schedule a factory tour. But if you can’t make it up there right now, our video is the next best thing.
*Stef again: Actually, you lost me at “fiberglass…”
That’s me (in the black shirt) helping move a Unity down the line. If that’s your TB… you’re welcome!
Comments